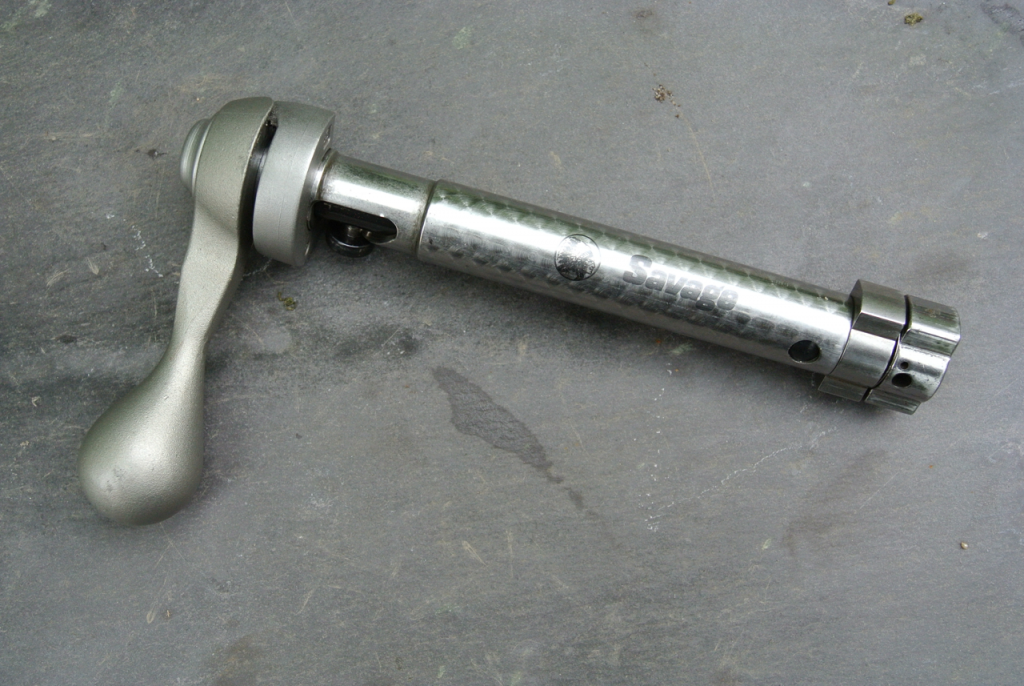
The Savage Model 12 action, which forms the basis of the Savage LRPV rifle and the FTR and Benchrest series of rifles, is quite exceptional – for a mass-produced, moderately priced, factory offering.
The action is available in several connotations – solid bottom, left or right bolt, dual port etc. and can be successfully used as the basis of a budget custom rifle. In long-range benchrest, we (UKBRA) have witnessed some remarkable performances from absolutely ‘out of the box’ factory Savage rifles – remember Scottish shooter David Sharp’s stunning 3.09 inch 5-shot 1000 yard group shot in an official UKBRA competition a couple of seasons ago?
Of course, the action is not perfect – the big weakness for me being the trigger. Alternative triggers are available – but not from the likes of Jewel or Bix n Andy etc. which is a great pity. And of course few, if any, factory actions will give you that ‘knife through butter’ feeling of a custom action when operating the bolt.
Now we’ve mentioned bolts, let’s take a closer look at the Savage bolt – it’s a bit different than most bolts in that it has a (removable) floating bolt-head. Not only can this be a handy feature if you wanted to swap cartridges/barrels but many noteable gunsmiths are convinced that it contributes to the accuracy of the Savage by allowing the bolt to maintain full lug-contact throughout the firing sequence. In any normal factory rifle, the bolt, when closed will be lifted ever so slightly by the trigger cocking piece, which will cause the bolt-lug, now in the 12 o’clock position, to lift off its seating in the action. More the bolt clearance in the action body and more the gap between the upper lug and its seating . A custom action will minimise this with a close-fitting bolt but with a sloppy factory fit……… On firing, the bolt is pounded hard against the lugs – which can set up a vibration and affect accuracy. The Savage floating bolthead maintains full contact throughout the firing sequence.
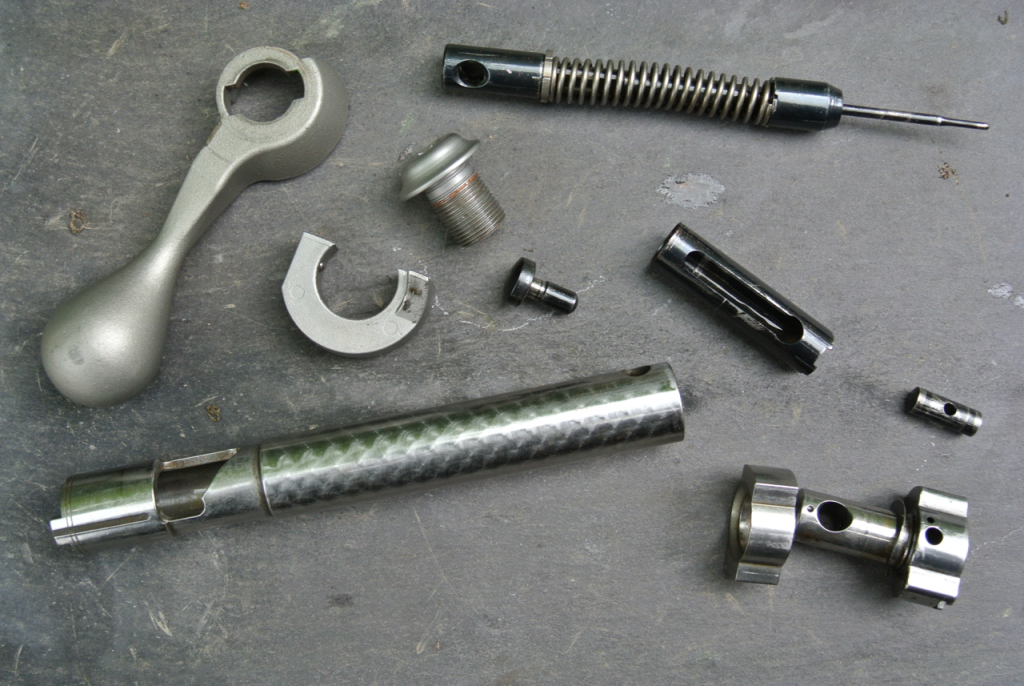
The Savage bolt has no less than 22 parts – or about twice the number in a Remington bolt. I’m convinced that this was originally designed to simplify production but, of late, one or two custom action manufacturers have copied the floating bolthead feature. But, some aspects of the Savage bolt design are not so clever and the cocking mechanism is ripe for a little improvement.
Benchrest shooters are always looking for a bolt which opens and closes with the least resistance – in other words with the least ‘upset’ to the rifle whilst operating the bolt. Any such upset will slow down the rate of fire by taking longer for the shooter to get back on his critical point of aim. Don’t forget, benchrest shooters usually fall into one of two categories – the pickers and the runners. The pickers will try and read the wind like an F Class shooter might but the runners will pick a wind ‘condition’ – which might only hold for 10 to 15 seconds and attempt to get off their five shots before the wind changes. This is where not upsetting the rifle between shots really pays dividends.
On any rifle, when the bolt is operated, a force is required to overcome the friction within the bolt and action which is of course added to by the fired cartridge case resisting extraction. BAT have now introduced a tiny roller bearing on the cocking-piece to reduce this friction – and very popular it is proving. It makes a really sweet action even sweeter!
Barnard use a single ball-bearing between the end-cap and firing-pin assembly to achieved the same effect and the RPA Quadlock with its Bellville washer assemble in place of a spring creates even more friction and RPA use a tiny flat needle-roller radial bearing on the end of the firing-pin assembly to reduce friction.
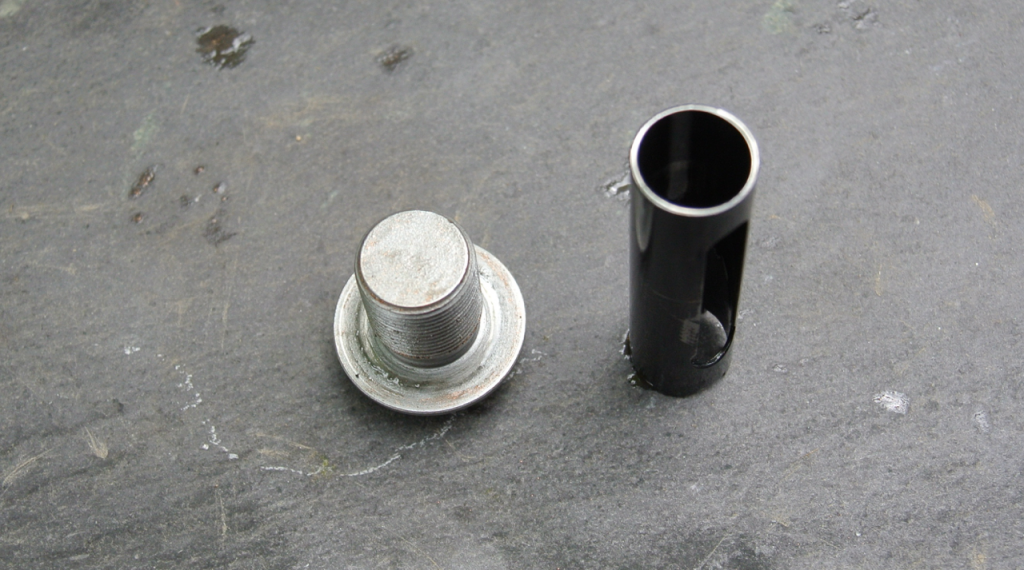
This friction is also present in the Savage action due to the cocking-sleeve/firing-pin assembly being in hard contact with the large bolt end-cap which holds the bolt together. Various ‘fixes’ have been attempted using the Barnard idea with a single ball-bearing but a better result can be achieved using a tiny ball bearing – see pic.
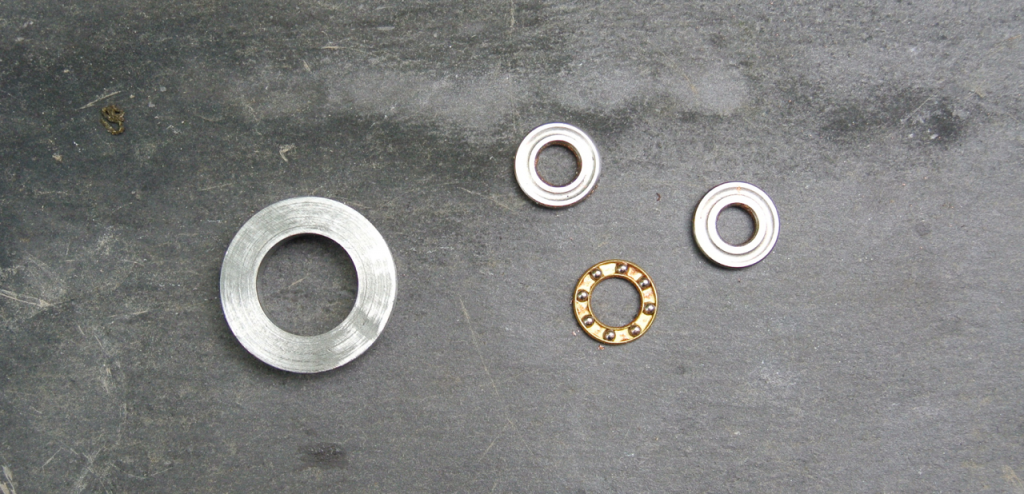
However, it’s not quite as simple as dropping in the bearing – the end cap needs to be shortened to compensate for the thickness of the bearing but, rather than attempt to shorten it, we simply made a stainless-steel spacer-washer the exact thickness of the bearing.
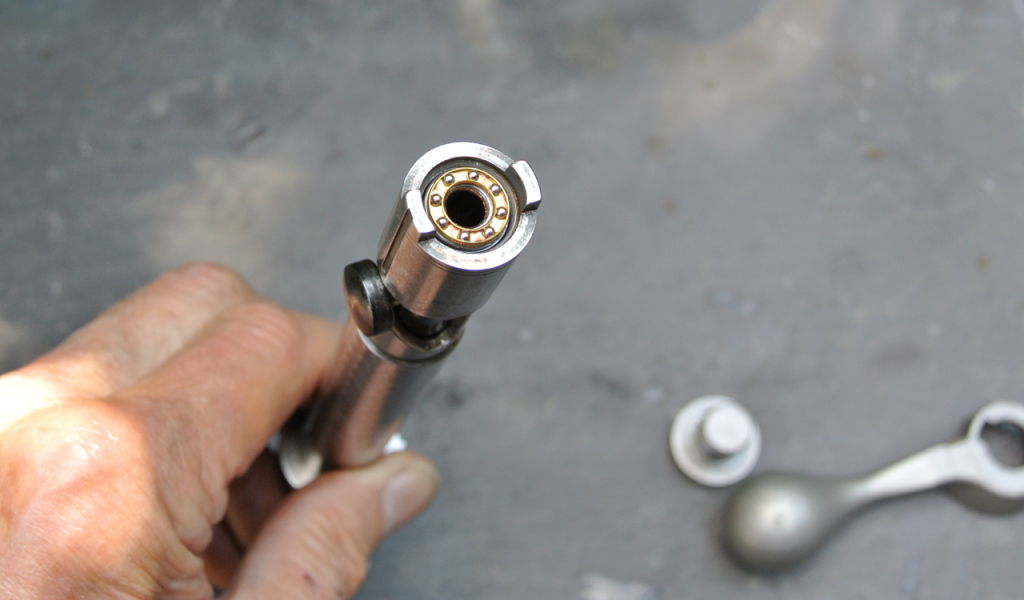
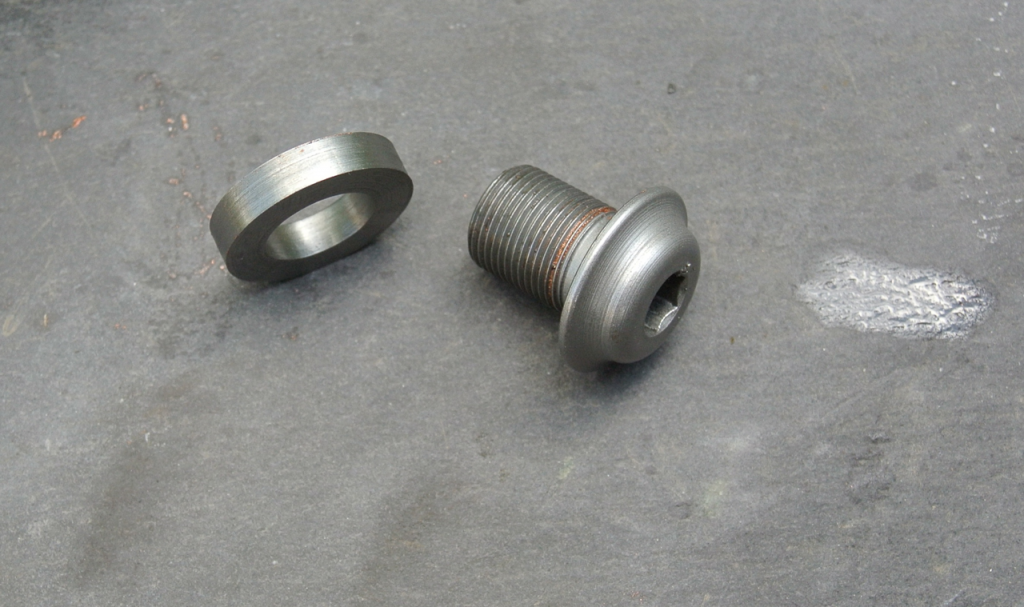
Does it work? Yes, the bolt is noticeably smoother in operation – not so much when dry-firing but certainly, under firing conditions, the bolt opens nicer, allowing the shooter to stay on target by not upsetting the rifle. Certainly, this is most useful in benchrest competition but who doesn’t love a ‘knife through butter’ action?
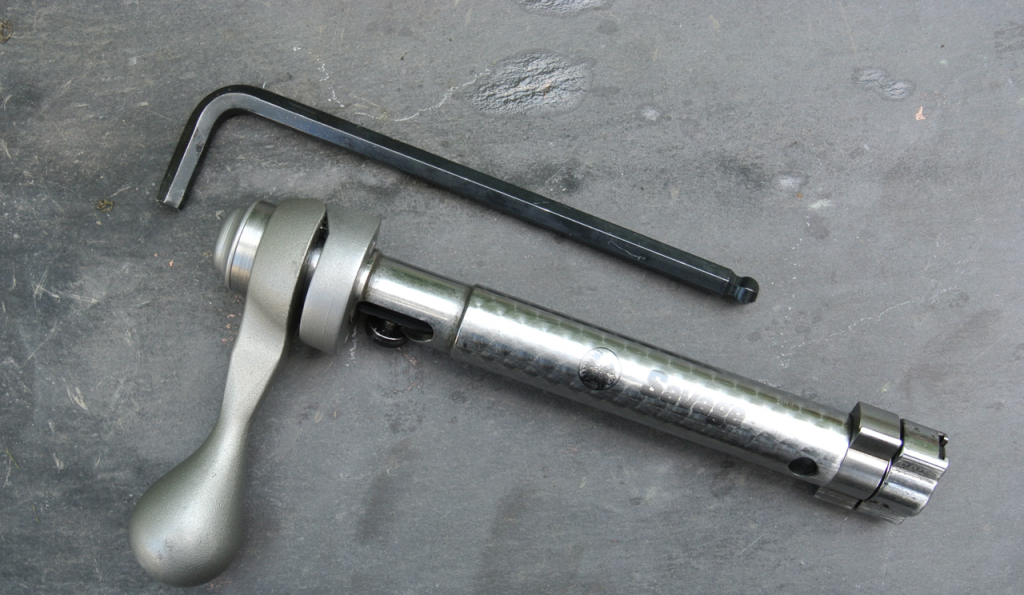